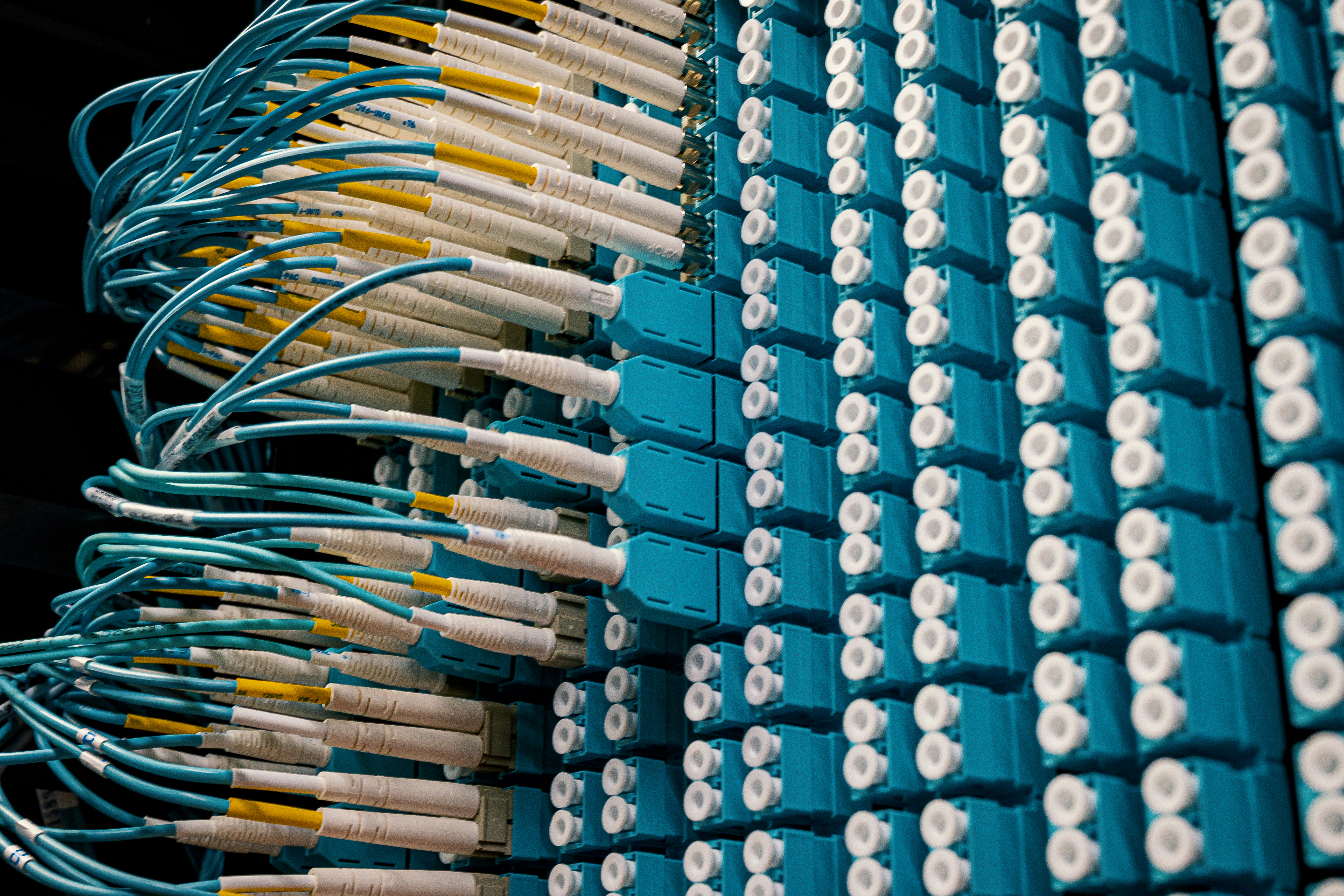
The technological impact of optical fiber on our communication system has been astounding. Many wonder how optical fibers are made. There are several steps involved in making an optical fiber, which include creating a preform glass cylinder, then drawing fibers from the preform. The following steps are general, with manufacturing processes varying per company and technology used.
OPTICAL GLASS
Optical fibers, a replacement for copper wires, come from an ultra-high-purity silica glass that can be stretched into long, hair-thin fibers and used to transmit information over long distances. Fiber optic strands consist of an inner core of high purity glass with a high refractive index that transmits light. These strands each feature an outer core of low refractive glass that keeps the light signal from seeping out the sides. The basic unit from which fibers are drawn is called a "preform."
PREFORM GLASS CYLINDER
A preform is a glass cylinder that might be several inches long and several inches thick. It has a different refractive index to provide the core and cladding of the fiber. The fiber's capability to reflect light is decided by the creation of the cladding glass, relative to the core glass. The reflection usually occurs by creating a higher refractive index in the core of the glass than in the surrounding cladding glass.
Modified chemical vapor deposition, which is a chemical process used for producing high-performance solid materials, is used for making the glass for the preform. Vapor deposition, outside vapor deposition, and vapor axial deposition, are the three methods usually used in this process.
The most common process used is the outside vapor deposition because it yields a low loss fiber that is very well suited for long-distance cables. This process is highly automated and usually takes several hours for completion. Once the preform blank is cool, it is tested for quality control and then placed into a fiber drawing tower.
DRAWING FIBERS FROM PREFORM
The drawing tower has a temperature of 3,452 to 3,992 degrees Fahrenheit or 1,900 to 2,200 degrees Celsius. This tower consists of a furnace that heats the tip of the blank until a piece of molten glass falls from the blank, pulling a thin strand of glass, which is the beginning of an optical fiber. Then the fiber goes through a monitor to ensure a specified outside diameter. Next, ultraviolet lamps are used for applying and curing coatings. The fiber is wound on spools at the bottom of the draw and each fiber is assigned a unique identification number. The optic fiber cables are formed by being coated, colored, and bundled in protective jackets.
Once the optical fibers are finished, they are tested for bandwidth, tensile strength, fiber geometry, operating temperature, range of humidity, refractive index profile, attenuation, and temperature dependence of attenuation. Cables that are going to be used undersea must have the ability to conduct light under the water.
FROM OPTICAL FIBER PRODUCTION TO MANY USES
The fibers, after they have passed quality control, are sold to many companies to improve capacity and speed, and to replace their old copper wire systems. Some types of companies that use fiber optics include network providers, telephone, power, and cable companies, and industrial plants.